What 300+ Engineers and Manufacturers Told Us About the Future of Quality

From real-time monitoring to predictive analytics and centralized data systems, discover how the manufacturing industry is (and isn't) embracing the Quality Revolution.
Unlock the Full Report
Form
The Tools Powering (and Hindering) Quality Progress
Quality work is evolving—but tools haven’t caught up.
We asked respondents what they use today to manage quality initiatives, SPC programs, and problem-solving projects.
The results showed significant fragmentation:
0%
47% use digital project management platforms (e.g., Asana, Jira)
0%
25% rely on Excel, Word, or SharePoint
0%
24% use internal, custom-built tools
0%
2% still use paper-based methods
Even among the digital adopters, tools often aren’t integrated, automated, or scalable.
Too many teams are doing digital work with analog tools. That’s creating data blind spots, delayed responses, and process inefficiencies that stall real progress.
Where Manufacturers Stand in Their Data Journey
The data is there. But it’s messy, fragmented, and hard to use.
Manufacturers are collecting more data than ever before—but collecting it isn’t the same as leveraging it.
When we asked how teams collect data for quality monitoring, we heard:
Yet despite all this input, only 26% say their data is immediately usable.
Key roadblocks:
- Data lives in different systems
- Manual cleaning or combination is required
- Teams don’t trust the completeness or accuracy of what they’re seeing
The future of manufacturing will be built on connected, clean, and centralized data systems. Many aren’t there yet—but they want to be.
0%
54% rely on operator entry
0%
36% use wireless sensors
0%
48% connect to controllers
0%
32% pull from cloud-connected machinery
What’s Fueling the Push Toward Real-Time Quality
Speed, pressure, and the rising cost of being too late.
Quality teams aren’t just looking for improvement—they’re looking for speed. In an increasingly competitive global market, delayed decisions cost money.
What’s motivating manufacturers to improve their processes?
0%
36% want to keep defect rates stable
0%
23% must meet quality demands as part of a larger supply chain
0%
17% are actively working to reduce defects
0%
14% are focused on minimizing downtime
These goals are difficult—if not impossible—to achieve without real-time feedback loops.
The shift toward real-time SPC isn’t just about monitoring—it’s about gaining the agility to act before problems grow.
Why the Future of Quality is Predictive
Manufacturers don’t just want to react. They want to anticipate.
We asked teams if they’re using predictive analytics or machine learning in their quality efforts.
- 30% use predictive analytics today
- 52% want to use them—but lack training
- 12% aren’t using them at all
- 6% want to—but don’t know where to begin
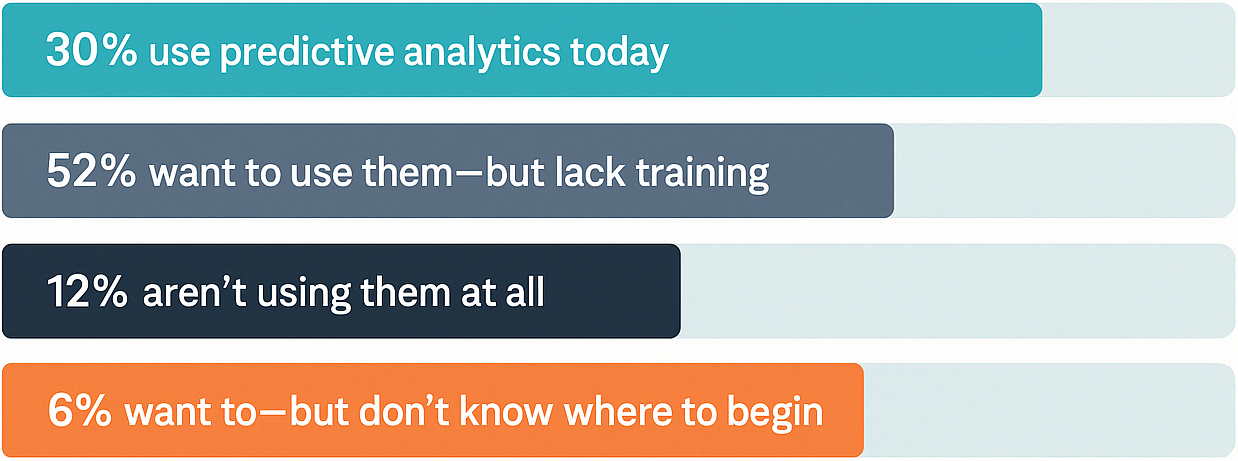
This tells us something important: the appetite is there. What’s missing is guidance, systems, and support.
Real-world use cases:
- Forecasting process instability
- Identifying root causes before issues spread
- Optimizing production based on historical trends
Predictive analytics can help move manufacturers from “monitoring quality” to actively shaping it.
Unlocking Quality at Scale
You can’t scale quality without solving visibility.
The most advanced quality teams aren’t just making improvements in one plant or one line. They’re building repeatable, scalable systems that work across facilities and teams.
What separates them?
Defects Decrease
Response Times Drop
Operator Trust Increases
Leaders Get Clearer ROI Visibility
If the tools work for one line—they should work for every line.
Unlocking Quality at Scale
You can’t scale quality without solving visibility.
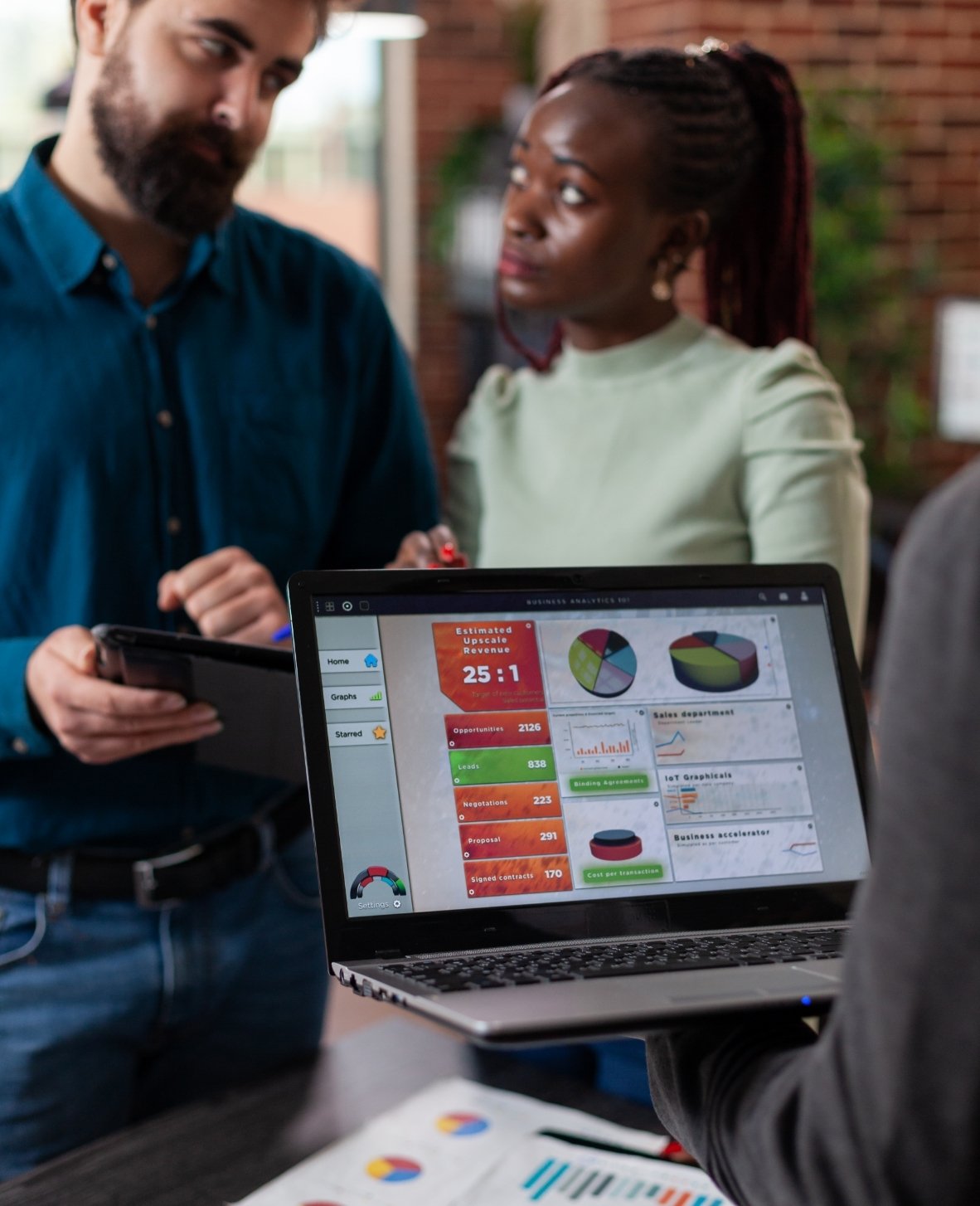
The most advanced quality teams aren’t just making improvements in one plant or one line. They’re building repeatable, scalable systems that work across facilities and teams.
What separates them?
What separates them?
- Connected dashboards that aggregate data across machines and shifts
- Alerts that trigger action, not just logging
- Automations that eliminate manual data entry and reduce variability
We’ve seen that once quality systems become centralized, everything changes:
- Defects decrease
- Response times drop
- Operator trust increases
- Leaders get clearer ROI visibility
If the tools work for one line—they should work for every line.
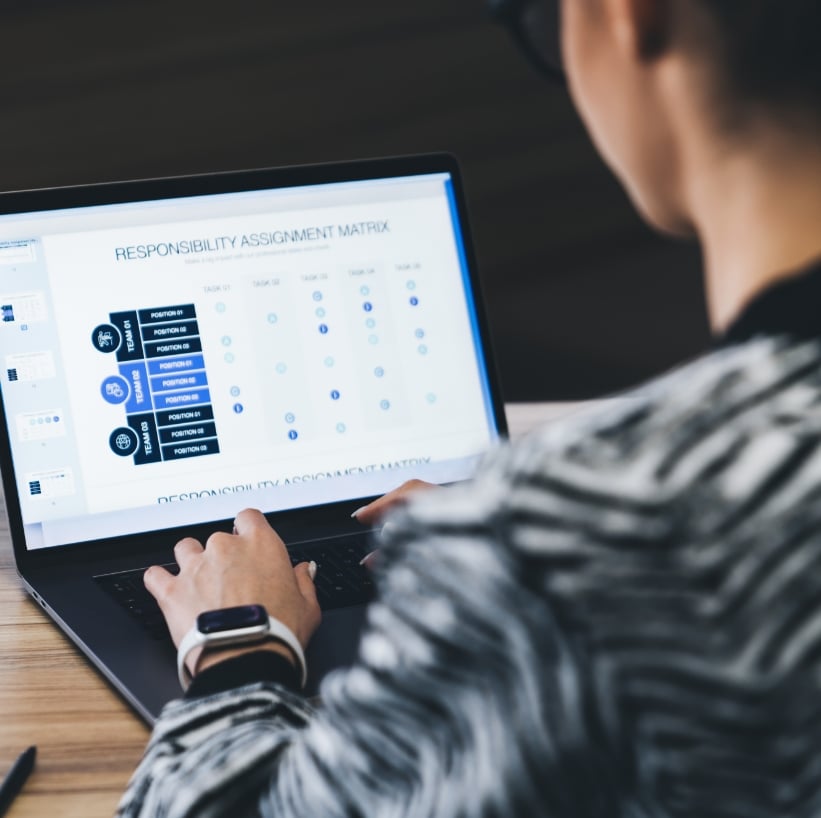
Embracing the Revolution: What Comes Next
The Quality Revolution isn’t a moment. It’s a movement.
The data is clear: teams are ready for better systems, faster insights, and deeper impact.
But readiness isn’t enough. What’s needed now is action—and alignment.
Here’s what quality leaders should prioritize:
- Break down data silos
- Automate data collection wherever possible
- Invest in centralized platforms
- Shift from reactive monitoring to proactive decision-making
The Solution: Real-Time SPC in Action
Introducing Minitab Real-Time SPC
Minitab Real-Time SPC gives you:
- Live dashboards that monitor every line
- Automated alerts when control limits are breached
- A centralized hub for plant-wide visibility
- Seamless integration with your existing equipment and databases
Perfect for:
- Reducing waste
- Meeting supplier quality agreements
- Minimizing downtime
- Scaling improvement across sites
It’s not just SPC. It’s visibility, accountability, and improvement—built into every shift.